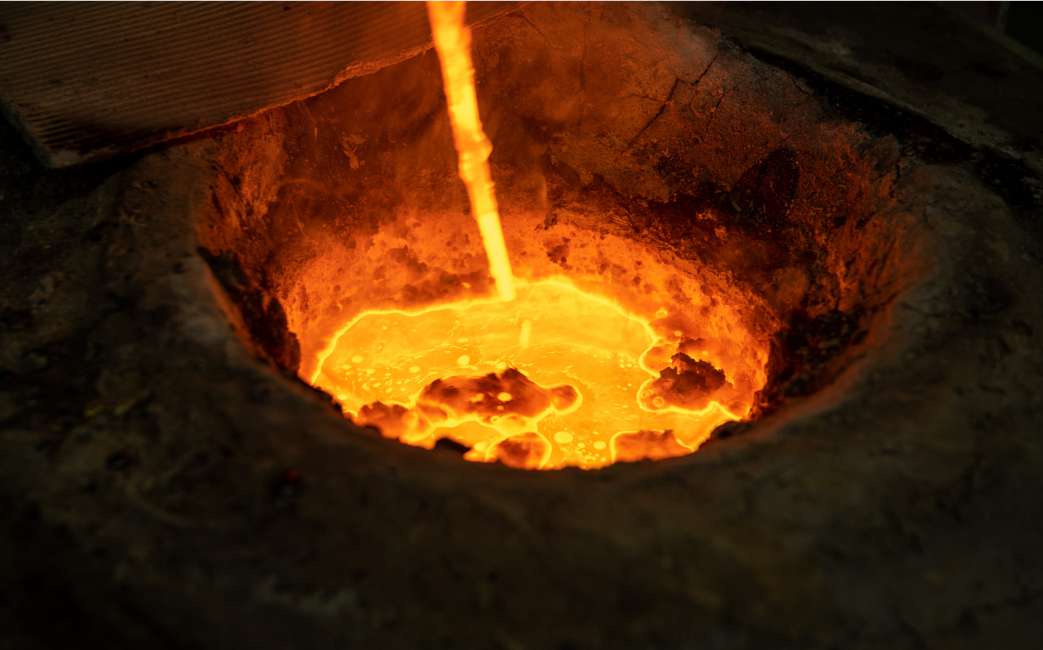
Сделано в Политехе
О новых разработках литейщиков Самарского политеха
Сделать сложную деталь для команды центра литейных технологий уже давно не проблема, потому что производство отлажено до автоматизма. А вот оптимизировать процесс, сделать его дешевле, а саму деталь более качественной – задачи, требующие творческого подхода, ведь для их решения необходимы абсолютно новые технологии. И вот тут литейщикам Политеха не обойтись без инженерной фантазии.
Доходы из отходов
Как правило, фасонные отливки (заготовки или готовые изделия), получаемые из первичных металлов, очень дорогие. Но специалисты центра литейных технологий (ЦЛТ) Политеха сумели не только снизить их стоимость, но и повысить качество. А потребовалось всего лишь сократить количество дорогостоящей лигатуры (это основной компонент для приготовления сплава, задающий свойства будущего изделия) за счёт рационального использования отходов производства.
– На предприятиях накапливается большое количество отходов. Благодаря нашей технологии можно максимально и эффективно вовлечь их в производство, – отмечает доктор технических наук, декан факультета машиностроения, металлургии и транспорта (ФММТ), руководитель научной группы Константин Никитин. – Каждый элемент шихты (исходной смеси компонентов, необходимых для сплава) содержит в себе определённую структурную информацию, которая в результате плавления «по наследству» передаётся рабочим сплавам и литым изделиям из них. Соответственно, от качества шихты зависит качество готового изделия. Конечно, многообразие структурной информации в многофакторной системе «шихта – расплав – литое изделие» затрудняет понимание механизмов модифицирования и управление ими. Но нам удалось в них разобраться.
Наши литейщики провели эксперименты по получению двух видов сплавов (Al–Si–Mg и Al–Mg) из разных вариантов шихты.
Сначала расплав Al–Si–Mg приготовили только из первичных металлов (более чистых, то есть с минимальным количеством примесей, но при этом более дорогих), а потом – из металлических отходов. В качестве «заменителей» чистого алюминия учёные использовали проволоку, оставшуюся после электротехнических работ, а вместо лигатуры – алюминиевые банки.
Что касается второго сплава (Al–Mg), то оба варианта его «рецептуры» включали отходы. Разница в том, что в одном случае они были литыми, а в другом – деформированными,
в виде пластин.
Проведённые эксперименты показали, что сплавы, в основе которых – правильно подобранные и подготовленные отходы, более качественные.
– Всё дело в структурной наследственности металлов и сплавов, – поясняет Никитин. –При переплавке отходов, например, баночных, по традиционным технологиям выход годного металла невелик. Но так как в своё время они прошли сильное деформационное воздействие, то структура их мелкодисперсная. Нам удалось её сохранить и через расплавленное состояние транслировать в твёрдую фазу, то есть в литое изделие.
Получается, что чем более измельчённой структурой обладает исходный материал для будущего расплава, тем выше будут физико-механические свойства готового изделия. Поэтому политеховцы берут определённое количество подготовленных к переплаву деформированных отходов и за счёт этого вводят меньшее количество дорогостоящей лигатуры. Так наши специалисты экономят, а также повышают срок службы и эксплуатационную надёжность металлических деталей.
Качество – в слоях
Для изготовления деталей сложной конфигурации удобнее всего применять технологии аддитивного производства. При существующем подходе к этому процессу в качестве основного материала берут металлические порошки и, с помощью лазера послойно спекая их, формируют будущее изделие. По словам наших учёных, технология эта далека от совершенства: дорого и подходит только для печати небольших партий. Для массового производства Никитин и его команда предлагают использовать метод послойной электродуговой наплавки, где в качестве главного компонента выступает металлическая проволока.
Способ послойной электродуговой наплавки заключается в том, что проволока расплавляется под действием электрической дуги и, касаясь металлической подложки или предыдущего затвердевшего слоя, быстро застывает и охлаждается. За счёт этого формируется микродисперсная литая структура. А значит, механические и эксплуатационные свойства изделия будут на высоте. Однако нередко на производстве получают детали с такими дефектами, как газовые и усадочные поры, несплавленные слои. Плюс к этому, так называемые градиентные параметры (температура дуги, интенсивность теплоотвода, скорость охлаждения) могут привести ещё и к искажению геометрии детали. И здесь решающее значение имеют правильно подобранные режимы процесса наплавки, усовершенствованием которых сейчас занимается команда Никитина.
– Сегодня одно из наших перспективных направлений – разработка технологии получения с помощью метода послойной электродуговой наплавки протяжённых (крупногабаритных в одном измерении) заготовок на основе алюминиевых сплавов, – отмечает Никитин. – Сейчас проводятся исследования с использованием сварочной проволоки Al-5%Si.
Мы определили оптимальную силу тока сварочной дуги, при которой кремний распределяется равномерно в алюминиевой матрице по высоте наплавленного слоя, формируется однородная микроструктура, необходимые плотность, микротвёрдость и, как следствие, оптимальное сочетание предела прочности, относительного удлинения и предела текучести.
В планах у команды Никитина – разработка гибридной технологии изготовления деталей из алюминиево-кремниевых и алюминиево-магниевых сплавов. Наши специалисты хотят совместить 3D-технологии с традиционными методами механической обработки. Если им это удастся, то в Политехе начнут выпускать готовые изделия по новой технологии.
Учёные уже заручились поддержкой Российского научного фонда. Их проект «Исследование процессов формирования структуры и свойств материалов, полученных электродуговой наплавкой для производства деталей из алюминиевых сплавов в аэрокосмической промышленности» в марте выиграл региональный конкурс «Проведение фундаментальных научных исследований и поисковых научных исследований малыми отдельными научными группами».
Не только, но и…
В этом учебном году специалисты ФММТ могут гордиться достижениями и в других сферах. Рассказываем о трёх наиболее ярких проектах.
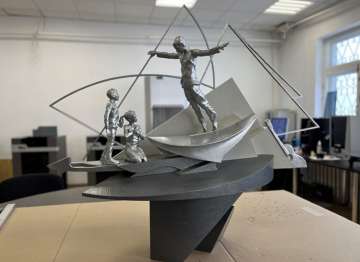
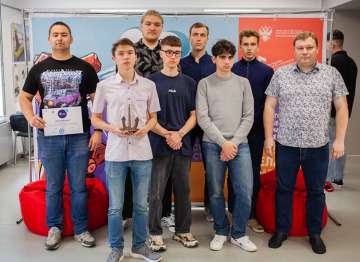
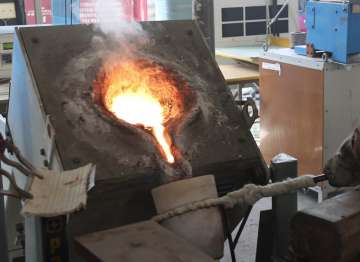
- Мастер-модель памятника Валерию Грушину
Литейщики Политеха помогли московскому архитектору Константину Прейсу создать скульптурную композицию, посвящённую героическому подвигу Валерия Грушина, который в августе 1967 года ценой своей жизни спас детей, утопающих в реке Уда Иркутской области. За 20 дней ведущий инженер центра литейных технологий Антон Баринов, инженер Дмитрий Соломатин и магистранты Константин Денисов и Владимир Константинов изготовили с применением аддитивных технологий мастер-модель будущей композиции.
– Нам нужно было не только разработать модель объекта, но и сделать так, чтобы его элементы после презентации и утверждения послужили основой для создания изделия в тех материалах (алюминий, песчаник, бетон) и тех размерах (пять на шесть метров), которые задумал автор, – поясняет Константин Никитин. – По математическим моделям Константина Прейса наши специалисты разбили композицию на части для удобства транспортировки и продумали элементы крепления, чтобы её можно было собрать воедино. Затем разработали управляющие программы для 3D-печати каждой из частей и, собственно, напечатали их. Наконец, полученные детали прошли финишную обработку (зачистку, грунтовку, покрытие специальной краской под цвет алюминия) и итоговую сборку. Масштаб нашей демонстрационной композиции – 1:5.
Теперь на основе мастер-модели, созданной политеховцами, памятник воплотят в металле и камне и установят в Новокуйбышевске, в сквере рядом с домом, где в середине прошлого века жила семья Грушиных.
- Судовой якорь Холла
Инженеры Политеха проводят работы по заказу самарского судостроительного и судоремонтного завода ЗАО «Нефтефлот». Так, студенческая проектная команда ФММТ под руководством доцента кафедры «Металловедение, порошковая металлургия, наноматериалы» Дмитрия Майдана с использованием современных инструментов разрабатывает технологический процесс производства судового якоря Холла.
– Мы применяем цифровые средства проектирования и моделирования, технологию 3D-печати, литейные технологии, – рассказывает Дмитрий Майдан. – Уникальность нашей разработки в том, что сначала создаётся цифровой двойник изделия сложной формы, а затем на основе цифровой модели на 3D-принтере печатается полимерная литейная модель необходимого размера. В дальнейшем по этой модели мы получим литую заготовку (отливку) из необходимого металла.
Студенты сделали в бронзе уменьшённую копию якоря, которая была вручена генеральному директору ЗАО «Нефтефлот» во время церемонии торжественного спуска на воду промерного судна «Створ» проекта RDB 66.62. Оно предназначено для 3D-сканирования глубины и рельефа дна с использованием многолучевого эхолота.
Кстати, в новом учебном году из студентов 3 курса ФММТ будет сформирована специализированная группа для обучения по программе «Кораблестроение». Ребята, успешно завершившие обучение, получат второй диплом, подтвердающий дополнительную профессиональную подготовку. В процессе обучения им будет выплачиваться стипендия от предприятия, а после защиты дипломов их ждёт гарантированное распределение на ЗАО «Нефтефлот».
- Программа целевого обучения «Инженерный старт – Металлургия»
В Политехе большое внимание уделяют формированию кадрового потенциала промышленных предприятий региона. Так, в этом году было принято решение о расширении совместного с ПАО «ОДК-Кузнецов» образовательного проекта «Инженерный старт». Теперь наш университет будет готовить для завода металлургов узкой специализации.
– В связи с увеличением на предприятии заказов на газотурбинные двигатели возрастает и потребность в специалистах по производству лопаток (лопастей) для этих двигателей. Размещённые в турбине лопатки работают в крайне напряжённых условиях, при высоких температурах и, соответственно, должны отвечать строгим требованиям качества. Поэтому и технология их производства достаточно сложная и специфичная. В России сейчас целевым образом таких специалистов не готовят ни в одном университете, ведь вузы должны выпускать студентов с широким знаниями и умениями в рамках выбранного направления подготовки, а эта деятельность слишком специфичная, но крайне востребованная, – говорит Константин Никитин.
Таким образом, в новом учебном году 12 абитуриентов поступят на бюджетные места, став участниками программы целевой подготовки «Инженерный старт – Металлургия» по профилю «Литейное производство чёрных и цветных металлов». Специально для них педагоги ФММТ совместно со специалистами предприятия разработают расширенный курс по технологии изготовления лопаток. Студенты смогут получать дополнительную стипендию от «ОДК-Кузнецов», пройдут производственную практику на заводе, выпускникам гарантируют дальнейшее трудоустройство.